Control valves are critical components in various industrial processes, ensuring efficient management of fluid flow, pressure, temperature, and level. They play a pivotal role in industries such as oil and gas, chemical, water treatment, and power generation. Selecting the right type of control valve for a specific application involves understanding their mechanisms, features, and applications. This article explores some of the most prevalent types of control valves used in industry, providing insights into their functionality and suitability for different operational needs.
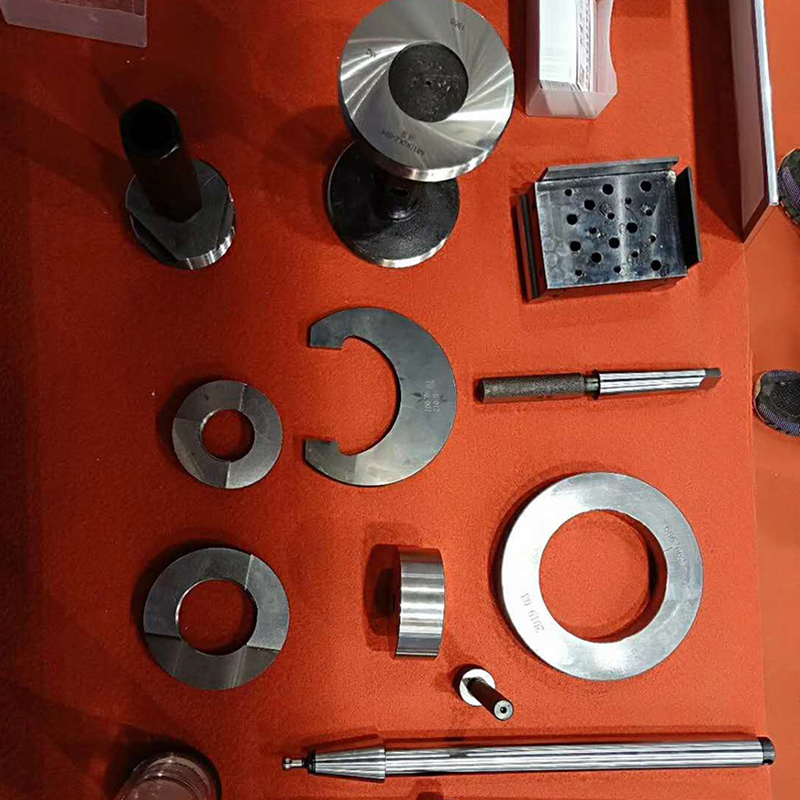
Globe Valves
Renowned for their excellent throttling capabilities, globe valves are commonly employed in applications where precise flow control is essential. Their design ensures a linear motion of the disk to regulate fluid flow, making them ideal for systems where frequent adjustments are necessary. Industries appreciate globe valves for their robust construction, which withstands high pressure and temperature. However, their flow path may cause a significant pressure drop, which must be considered during system design.
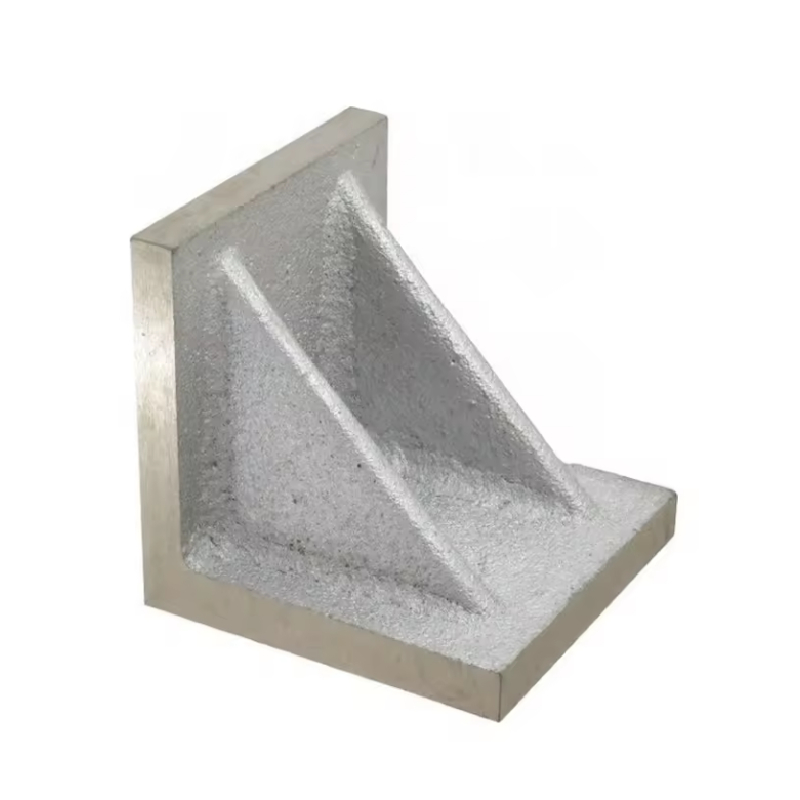
Ball Valves
Ball valves are extensively used due to their simplicity and efficiency in providing tight shutoff. The spherical disc design allows for quick opening and closing, making them ideal for applications requiring rapid response times. They are versatile, handling a range of pressures and temperatures. Their durability and low maintenance requirements make them a popular choice in oil and gas pipelines and water distribution systems. Nevertheless, ball valves are less suited for precise flow control, often leading to cavitation if not properly calibrated.
Butterfly Valves
These valves are recognized for their compact design and cost-effectiveness, making them a preferred choice in large-diameter pipelines. Butterfly valves use a rotating disk to start, stop, or modulate flow, offering minimal resistance and a lower pressure drop compared to globe valves. They are extensively used in water treatment, chemical, and HVAC systems. Despite their advantages, butterfly valves may not provide the same level of tight shutoff as ball valves, which should be considered when selecting a valve for critical isolation applications.
Diaphragm Valves
types of control valves used in industry
Diaphragm valves excel in applications where corrosion resistance and contamination prevention are paramount. Their unique design involves a flexible diaphragm that comes into contact with the fluid, making them ideal for handling slurries, corrosive chemicals, and high-purity applications. Industries such as pharmaceuticals and food and beverage highly value diaphragm valves for their ability to ensure hygienic processing. While they offer superior sealing capabilities, they may not be suitable for high-pressure applications.
Check Valves
Check valves are essential for preventing backflow, ensuring that fluid flows in a single direction. Their automatic operation is governed by the flow of the fluid itself, requiring no external control mechanism. They are vital in protecting equipment and preventing contamination in water and wastewater systems, pump stations, and process industries. It’s crucial to select the appropriate type of check valve, such as swing, lift, or ball check, based on the specific requirements of the operation to avoid issues like water hammer.
Control Valves with Actuators
Incorporating actuators in control valves enhances automation and precision in myriad industrial processes. Pneumatic, electric, and hydraulic actuators convert control signals into mechanical motion, allowing for remote and accurate modulation of the valve position. This integration is crucial in modern industries seeking increased efficiency and reliability in their operations. Selection of the right actuator depends on factors like power availability, speed of operation, and control precision required.
Conclusion
Choosing the appropriate type of control valve is a strategic decision that influences the efficiency, safety, and reliability of industrial systems. Understanding the strengths and limitations of each valve type is essential for engineers and maintenance teams tasked with optimizing process performance. By considering the specific operational requirements and environmental conditions, industries can leverage the right combination of control valves to achieve seamless and effective process control, driving productivity and sustainability in their operations.