Choosing the right valve fittings is essential in ensuring the efficient performance and longevity of fluid handling systems. Among these, the butterfly valve fitting stands out as a pivotal component used across various industries due to its simple yet effective design, versatility, and durability. With years of experience in industrial fluid systems, I’m here to provide an expert insight into the world of butterfly valve fittings, emphasizing their application, benefits, and the reason why they are a staple in system optimization.
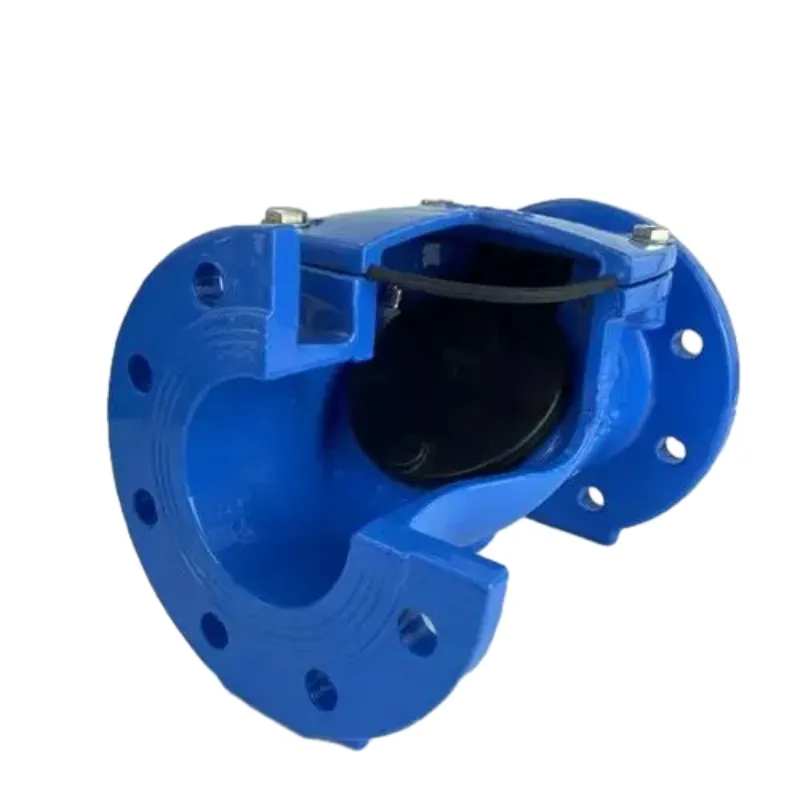
Butterfly valve fittings are distinctive for their disc-based operation mechanism. The design allows them to regulate flow easily, a feature primarily utilized in systems that handle large volumes of fluid or gas. The valve's disc or butterfly rotates around its axis, enabling precise control over the flow, making it optimal for applications needing reliable modulations, such as in HVAC, water treatment, chemical, and even firefighting systems.
From an expert perspective, the materials used in the crafting of butterfly valves are as critical as their design. Depending on the application, they can be made from stainless steel, cast iron, PVC, or even exotic alloys for hazardous applications. Each material has unique properties affecting the valve's overall resistance to pressure, temperature, and corrosive elements. For instance, stainless steel valves are preferred for their corrosion resistance and strength, crucial for harsh environments often found in chemical processing plants.
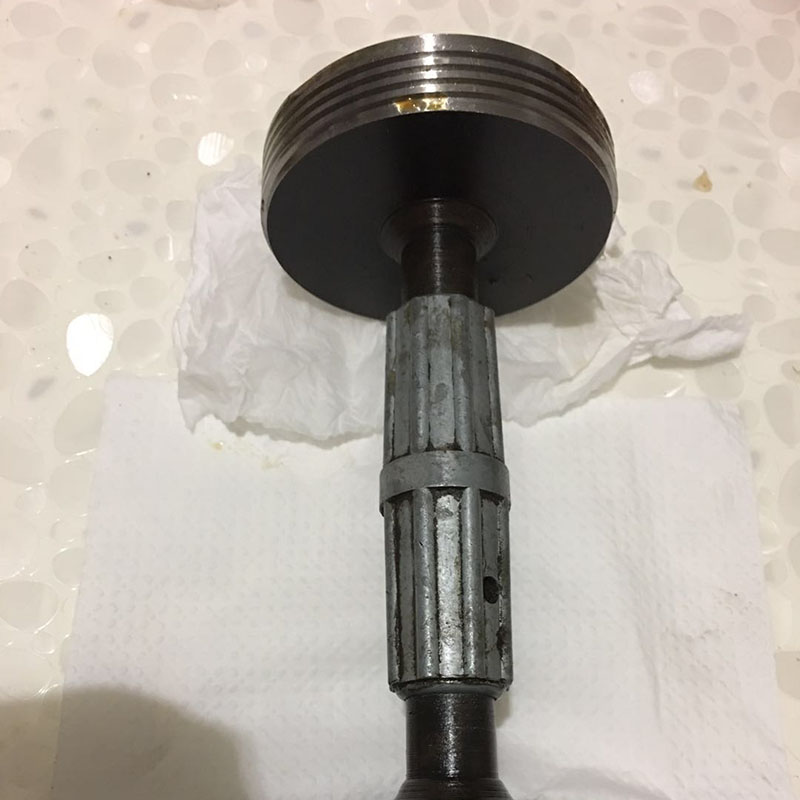
The installation of butterfly valve fittings is straightforward, contributing to their popularity. These valves are available in wafer and lug styles. The wafer style is secured between pipe flanges through bolts, providing a tight seal, ideal for situations where space-saving is critical. On the other hand, the lug style offers more stability and is beneficial for end-of-line service applications where dismantling a section of the pipeline is anticipated for maintenance or expansion.
Trustworthiness in the performance of butterfly valves cannot be overstated. They are engineered to ensure a high degree of durability and reliability. Manufacturers often subject these valves to rigorous quality control standards. The validation may include pressure testing, temperature endurance, and longevity assessments. Such testing ensures that the valves not only meet industry standards but also adhere to strict safety protocols. Always looking for industry certifications, like ISO or ANSI, can further assure buyers of the quality and reliability of their chosen fittings.
butterfly valve fitting
In terms of expertise, understanding the flow characteristics that butterfly valves bring to a system is essential. They offer a quick shut-off function while maintaining a low-pressure drop, an aspect crucial in energy efficiency. Lower pressure drop translates to less energy required to move the fluid, which can lead to significant cost savings in large-scale operations over time. The size of the valve also matters; butterfly valves typically range from 2 inches to several feet in diameter, allowing selection to meet the exact specifications and requirements of your system.
Moreover, current advancements in technology have allowed for the integration of automation within butterfly valve fittings. These include electric or pneumatic actuators that enhance control precision, reduce the need for manual operation, and facilitate integration with smart systems for real-time monitoring and adjustments. Such tech integration is beneficial in maximizing system efficiency and reducing human error.
Finally, situations of concern may arise about potential leakages, a common worry with valves. Butterfly valve fittings are designed with a variety of seat materials like EPDM, PTFE, or Viton, each suited to different operating conditions and media types, to ensure they maintain excellent sealing capabilities. Regular maintenance and routine checks are generally recommended to preserve their optimal performance and extend the service life.
In conclusion, butterfly valve fittings are indispensable in modern fluid systems due to their simplicity, economic benefit, and reliability. Whether ensuring successful applications in robust industrial environments or integrating seamlessly with smart technology, these fittings uphold a standard of engineering excellence. Their design and functional capabilities make them a preferred choice, adding significant value to any system they are part of.